Engineering and Instrumentation
Equipment Failure Analysis and Prevention
Why Attend
The prevention of potential damage to machinery and equipment is necessary for a safe and reliable operating plant. This course will provide participants with International Standards Organization (ISO) references, Operational Excellence Standards and best practices used in failure analysis and prevention. Failure analysis is a critical aspect of product development, as well as of component and system improvements. Every product or process has modes of failure which can be analyzed using tools such as Failure Modes & Effects Analysis (FMEA), Failure Modes, Effects & Criticality Analysis (FMECA), Event Tree Analysis (ETA), Fault Tree Analysis (FTA), and Risk Based Maintenance (RBM).
Participants will learn techniques, tools and the procedures of root cause failure analysis and failure mode effective analysis as a proactive strategy for achieving precise operation, and improving machinery performance. This course offers an insight into how to analyze a system’s failure modes and define how to prevent or find those failures early.
Course Methodology
The course is interactive and is comprised of presentations, case studies, technical process learning and supplemental discussions related to various industries and the challenges of implementation.
Course Objectives
By the end of the course, participants will be able to:- Implement the latest best practices in failure analysis
- Understand how criticality assignment and prioritization assists maintenance of machinery
- Identify equipment criticality and functional failure
- Utilize Risk Based Maintenance (RBM), Root Cause Analysis (RCA), and Fault Tree Analysis tools
- Explain life cycle cost analysis and evaluation
Target Audience
This course is designed for Technical Authorities (TAs), Reliability Engineers, Production/Operation Engineers, Maintenance Engineers, Design Engineers, Planning Engineers, as well as other maintenance personnel and anyone who would gain from understanding how the failure analysis and prevention function interacts within their roles and responsibilities.
Target Competencies
- Root Cause Analysis
- Failure Modes and Effects Analysis
- Fault Tree Analysis
- Risk Based Maintenance
- Maintenance Management
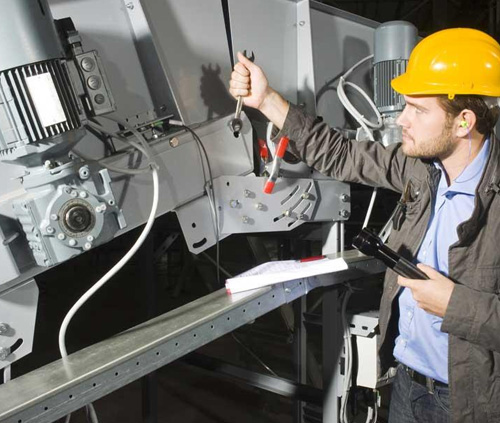
Course Outline
- Introduction To Failure Analysis
- Failure Analysis and troubleshooting as a tool for machinery reliability
- Causes of Machinery Failure
- Machinery Design Properties
- Equipment Failure
- Types of Failure Causes
- Effect of Failure
- Failure Cascading, Modes and Reduction Programs
- Life Cycle Cost Evaluation
- Reliability Centered Maintenance (RCM) and Root Cause Failure Analysis (RCFA) Process
- What is RCM?
- What is RCFA? Why is it done?
- Types of Root Causes
- Challenges in Setting up RCFA
- Sustaining an RCFA Process
- Failure Analysis and Investigation Tools
- Fishbone Diagrams, Pareto Charts, Fault Tree Analysis and Events Tree Analysis
- Failure Mode and Effect Analysis (FMEA)
- Failure Analysis Methods and Techniques
- Implementing FMEA and FMEA Procedure
- Risk Management and Failure Analysis
- Predictive Maintenance and Condition Monitoring
- Machine Failure Modes
- Equipment Performance
- Methods of Detection
- Machine Failure
- Structured Problem-Solving Techniques Risk Management
- Hazard and Operability (HAZOP)
- HAZID (Hazard Identification)
- Machine Reliability
- Reliability & Maintainability
- Techniques & Analysis of Reliability
- System & Human Reliability
- ISO Standards
- Auditing & Review Machinery Reliability
REQUEST CALL BACK
Would you like to speak to one of our consulting advisers over the phone? Just submit your details and we’ll be in touch shortly.
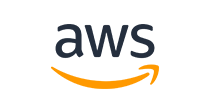
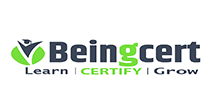

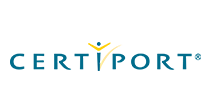










