Procurement and Supply Chain Management
Production Management and Material Requirements Planning
Why Attend
The overall aim of this course is to provide participants with the knowledge, skills and techniques needed to perform all the essential tasks in a production environment. The course includes important concepts such as forecasting demand, capacity planning, determining requirements and scheduling. Participants in this interactive course will learn all the critical processes, formulas and calculations required to manage production systems effectively.
Course Methodology
This course relies on the use of individual and group exercises aimed at helping participants learn all production planning activities. The course also features the use of a number of case studies followed by discussions. In addition, this course incorporates pre and post testing.
Course Objectives
By the end of the course, participants will be able to:- Construct a framework for production planning and demonstrate how it fits within the supply chain context
- Create forecasts for the expected demand on an aggregate level and use them as a basis for all future planning and scheduling
- Estimate and control the capacity requirements and the optimum utilization of the resources
- Assemble and manage sales and operations plans and develop chase and level production strategies using time phased grids
- Identify optimum inventory level, lead time, re-ordering point and production quantities
- Develop a detailed master production plan that shows the timing and the quantity of planned production and establish material requirements planning system based on the master plan
- Generate performance measurement indicators for a production system
Target Audience
Professionals involved in any production or operation facility and interested in learning about all the important aspects of a production environment including planning, scheduling, forecasting and production management.
Target Competencies
- Forecasting demand
- Strategy planning
- Decision making
- Planning and scheduling
- Inventory management
- Production management
- Material requirements planning
- Performance measurement
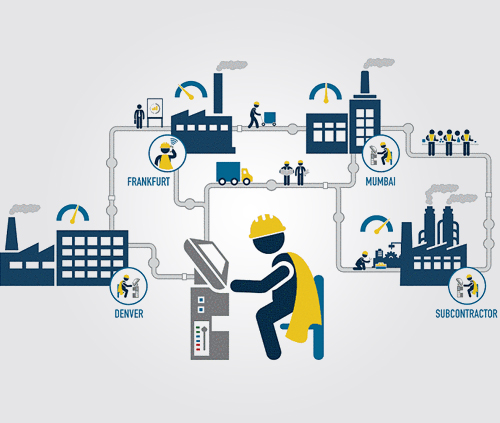
Course Outline
- Production Planning and Control (PPC)
- Defining production planning and control
- Areas of influence on PPC
- A framework for a PPC system
- PPC systems activities
- Productivity in production environment
- Demand management
- Demand management in PPC systems
- Independent and dependent demand
- Forecasting framework
- Forecasting techniques
- Evaluating forecasts
- Capacity planning
- Measuring capacity
- Capacity utilization
- Calculating capacity requirements
- Cost volume analysis
- Break even analysis
- Decision tree
- Sales and Operations Planning (S&OP)
- S&OP fundamentals
- S&OP displays
- Time phased planning
- Modifying the S&OP
- The basic trade-offs in S&OP
- Evaluating alternative plans
- Inventory management
- Types of inventory
- Inventory costs
- Economic order quantity model
- Inventory order cycle
- Reorder point
- Economic production quantity
- Multi criteria ABC analysis
- Requirements planning and scheduling
- Master production scheduling activities
- Master production scheduling techniques:
- The time phased record
- Available to promise
- Material Requirements Planning (MRP)
- Bill of material
- MRP processing
- The basic MRP record
- Material planning for:
- Lot-for-Lot
- Different lot sizes
- Performance measurement
- Key performance indicators
- Benchmarking and standards
- Measuring performance
- Improving current production system
REQUEST CALL BACK
Would you like to speak to one of our consulting advisers over the phone? Just submit your details and we’ll be in touch shortly.
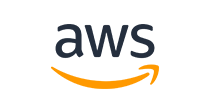
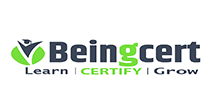

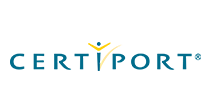










