Quality and Productivity
Certified Lean Six Sigma Green Belt
Why Attend
Join us to become a certified Six Sigma practitioner joining the thousands of Six Sigma professionals we have successfully trained over the last 20 years. Six Sigma is an industry standard methodology for process improvement and business transformation. Our IASSC accredited Green Belt course is well recognised for its comprehensive and robust content aligned with the international Body of Knowlege (BOK) by as ASQ and IASCC. This unique Green Belt Six Sigma course will help you to improve the quality of your company operations by adopting a data-driven approach and provide you with the skills necessary to work on projects to benefit all types of processes and businesses. Participants will learn the different phases of Define, Measure, Analyze, Improve and Control (DMAIC) and how to craft a project charter. Additionally, participants will learn about quality tools and statistics to help them formulate problem statements and translate them into a measurable format. Participants will be provided with the tools to assess their organization's readiness to launch Six Sigma projects.
Course Methodology
The course will present participants with the chance to practice the skills acquired through exercises and case studies. Group and individual presentations will also be conducted. Additionally, videos will be shown about real life companies which have implemented the Six Sigma methodology. A Case study will guide the training. Following the course, you will receive a Six Sigma Green attendance certificate. Certification will be obtained by passing an exam at the end of the course to measure the participants' knowledge on Six Sigma body of knowledge (BOK).
Course Objectives
By the end of the course, participants will be able to:- Improve processes using DMAIC Six Sigma (variation removal) and Lean approach (waste removal)
- Discuss Six Sigma and why it is necessary to sustain business improvement
- Apply and implement the Define, Measure, Analyze, Improve and Control problem-solving methodology
- Collect and analyse data appropriately using various tools in Minitab
- Apply various tools usually used in a Six Sigma project
- Understand how to scope a project and build a business case for management to deploy Six Sigma
Target Audience
Managers, supervisors and professionals who wish to fully utilize Six Sigma approach in their organizations, become certified professionals and learn how Six Sigma relates to work and business improvement.
Target Competencies
- Deploying Six Sigma
- Problem-solving skills
- Critical thinking skills
- Using applied statistics
- Lean principles
Note
Note1: Your Six Sigma Green Belt will include some pre-class work and reading, five days in the classroom and then further self-led study to reinforce what you’ve learned.
Note 2: Included in the course: A rich workbook that contains the slides and material, +40 useful Six Sigma and Lean templates, 30-day Minitab free trial and 2 hours of free coaching (by email) by the experienced trainer.
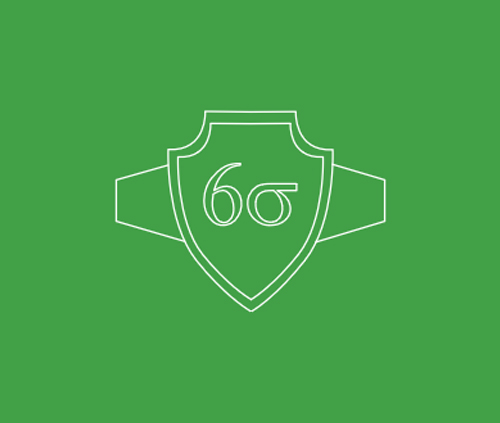
Course Outline
- Define Phase
- Understanding Six Sigma
- Six Sigma fundamentals
- Selecting projects
- Project charters and problem statements
- SIPOC followed
- Team creation, RACI and communications planning
- Voice of the customer / CTQs followed
- Project planning, risk assessment and project launch
- Elements of waste
- Measure Phase
- Process discovery
- Six Sigma statistics
- Measurement System Analysis (MSA)
- Process capability
- Introduction to Minitab
- Types of data and basic statsCentral Tendency, Variation and Tampering
- Graphical displays – Histograms, dot plots, box plots
- Process Mapping
- Data collection planning
- Measurement systems analysis and Gauge R&R
- Sampling
- Statistical Process Control (SPC)- Control charts
- Analyze Phase
- Inferential Statistics
- Introduction to Hypothesis Testing
- Hypothesis Testing Normal Data Part One and Part Two
- Hypothesis Testing Non-Normal Data Part One and Part Two
- Brainstorming and Cause and Effect diagrams
- Data analysis – Pareto charts, run charts, frequency charts
- Improve Phase
- Process Modeling Regression
- Advanced Process Modeling
- Designing Experiments
- Lean Tool box - Takt time, Kanban and Flow (Push v Pull), TPM,
SMED - Poka Yoka
- Evaluating and selection solutions
- Reducing complexity and Standardisation
- Pilot testing
- Control Phase
- Advanced Experiments
- Capability Analysis
- Lean Controls
- Defect Controls
- Six Sigma Control Plans
- Saving calculation – Cost of non-quality
- Project close out/handovers
- DMAIC summary
REQUEST CALL BACK
Would you like to speak to one of our consulting advisers over the phone? Just submit your details and we’ll be in touch shortly.
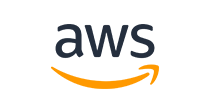
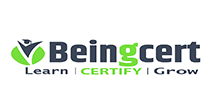

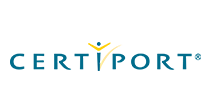










